Kori Chapic's Senior Thesis e-Portfolio
Construction Management Option
Cleveland Clinic Cancer Center
Cleveland, Ohio
Executive Summary
The following proposal introduces the research topics I would like to pursue as part of my senior capstone project next semester. Having an internship on the jobsite I am also conducting my capstone provides a lot of benefits for some of the project challenges from a personal standpoint as well as a more effective impact.
The first analysis consists of a redesign into an alternative support of excavation process. The Cancer did not have an issue with this system but personally learning that the system basically serves no purpose after the construction process and is eventually just buried leads in the opposite direction of LEAN design and wasteful practices.
The second analysis area deals with the project submittal process and determining an alternative process that could minimize the time it takes to approve these submittals. By expanding upon some of the ideas and issues that were addressed on the jobsite throughout my internship hopefully an all-encompassing solution could be devised that would minimize the approval duration for each submittal. Also having a submittal process that could have a submittal be approved the first time to eliminate multiple reviews.
The third analysis area would be to address the complex curtainwall system and devise an alternative system that aesthetically looks the same but has easier connections to the building. This alternative system would ideally also address the constructability issues of needing two full floors in order to place the system.
The research topic and industry issue I would like to address is one that came to fruition at the PACE round table discussion. In looking at LEAN design the idea of project turnover to facilities managemnt was addressed. In the construction process building materials, equipment, specifications, and functionality are all compiled electronically to then be handed over to the owner for future building use and management. Part of my research will identify how this isnformation transfer is conducted, the challenges of facilities management, and potential solutions that could optomize the transfer and future utilization of this information in facilities management. Furthermore, a gaming software, Unity, will be investigated to identify its capabilities and potential use in facilities management.
The proposal wraps up with a description of the breadth topics to further and more adequately address the analysis topics discussed above. The first breadth topic would be to discuss the structural requirements that would need to be satisfied in order to successfully have the support of excavation system serve as a foundation system as well. With this implementation the combined cost of the current support of excavation system and the current foundation system could be combined to provide a budget maximum for a combined system.
The second breadth I would like to pursue is an acoustical study in the office spaces and the infusion rooms. Because of the connection of the curtain wall to the interior partition walls the detail of this connection is very particular and could provide an acoustical gap between spaces. By looking at the before and after connection type and materials hopefully any acoustical gaps could be mitigated and these rooms can remain more private from strangers in neighboring rooms.
The overall goal is to have a building that is even better than the proposed processes. The assumptions made in this proposal are looking for further opportunities in construction not necessarily that the current system doesn’t work but rather that it may be addressing a different issue better than other potential issues.
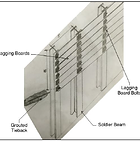
Analysis 1: Support of Excavation
Background research
As a large scope of the Cleveland Clinic Cancer Center project the excavation of the building footprint removed roughly 80,000 cubic yards of mixed soil and rock excavation. With the removal of this soil, the excavated area needed a support system for the entire perimeter of the building excavation. The dimensions of this soldier piles and lagging system would be roughly thirty to thirty-five feet deep at some locations and run a closed loop of approximately 1450 linear feet. The soldier pile and lagging process is done in stages to ensure proper excavation support and worker safety. At roughly ten feet and twenty-five feet a special machine is used to shoot reinforcing bar tiebacks into the soil to remain so that the soldier beam and lagging system does not collapse when the moment force from the excavation increases while the depth of the excavation increases.
The soldier pile and lagging system needs to be erected alongside the excavation. With these steps taking place this could cause a safety hazard with many activities in the same place and site congestion. Also overlapping trades could have a negative impact on the productivity of the crews.
This current system will also be completely buried and never serve a purpose after construction. The piles and the lagging boards, the tiebacks and grouted concrete will all be buried under the surface and serve no structural purpose after the basement construction is complete. This waste of materials should try to be addressed so that the project can be more LEAN and eliminate wasteful practices/systems.
Potential solution(s)
Considering the major impacts from this soldier pile and lagging excavation support system, some of the potential solutions for this system include changing the system to a concrete diaphragm or slurry wall, shotcrete tieback wall, interlocking steel sheet piles, or tangent auger cast piles to name a few (1). No matter what the alternative system is, it will most likely contain extensive labor crews, consists of multiple stages, consume a lot of time, and be a large expense to the project. The objective would be to compare the new system to the current system and find one that would improve the current duration, cost, and safety.
Methods
The process of replacing the current support of excavation system would begin with extensive research of alternative systems. Looking more in depth of the systems listed above and also researching other possible systems, a chart documenting the pros and cons of the different systems would have to be created and cross referenced.
Another step in the research process is to determine the soil type and pressure the system would need to hold to ensure the system would work. When cross referencing the specific existing site conditions, a priority checklist should be created and implemented of the most important factors the system needs to support all the way down to the least important factor. For instance, if it is discovered that one system cannot or should not be implemented for excavations deeper than ten feet that system would automatically be eliminated because our excavation depth is 25-35 feet deep.
The third step in this process would be to select the best system. After selecting, the details of the new support of excavation system would need to be planned out and a general process of implementation would need to be constructed. This would be necessary to plan a process and detailed sequence of events and estimated process duration to compare to the current duration of the soldier pile and lagging system. Another way to approach the schedule would be to determine the necessary equipment and crew sizes in order to match the current duration of the soldier pile and lagging system.
After determining the schedule impacts, a cost analysis could be computed to compare to the soldier pile and lagging system. Material, labor, and even cost of the schedule will all be considered in this analysis.
Throughout the cost and scheduling process safety will be assessed based on the crew sizes, the labor demands, and the overlapping of different trades.
Lastly, a decision whether the current soldier pile and lagging should remain based on the schedule, safety, and cost implications.
Expected outcome
It is expected that the system chosen is most likely the best system for this application. Although, overall the current soldier pile and lagging system may be the best, it can be predicted that an alternative system may have a faster duration, cheaper cost, and/or safer working conditions. Most likely not all three will be found but would be the most ideal outcome. With this assumption, addressing the owners concerns may only focus on one or two of the above factors that will outweigh the other factors.

Analysis 3: Curtain Wall Assembly
Background research
The glass curtainwall system on this project is roughly 80% of the building fenestration. Because of the large architectural impact the glass has on the building it would not be ideal to change the curtainwall and dramatically change the aesthetics of the current project. Rather than change the project aesthetically, a main goal of the curtain wall system would be to research similar performing curtainwall systems that did not have as complex connections to the interior walls of the building. The reason for the complex connections to the curtain wall and the interior walls is because the curtainwall needs to be able to move roughly one to one and a half inches because of wind, weather, and other issues pertaining to the system functioning.
Another issue that could be addressed with this system is the construction schedule. The curtainwall system requires 2 floors of the building in order to place the curtainwall system. With a crane on the floor above and the curtainwall laid on the floor above it leaves these two floors virtually impossible to have other trades on these floors and limits the accessibility of the site.
Potential solution(s)
By finding an alternative yet similar system aesthetically the connections from the curtainwall to the interior walls do not need to have as much coordination and could lead to a less problematic curtainwall system. Conducting proper research to determine the exact reason the wall needs to move would be a large beginning as to how to solve this issue with another proposed system.
Another aspect that could be addressed is if there are other alternative ways to construct the curtainwall system. Potentially finding a method that only needs one floor to properly place the system or even a system that could be placed by workers on lifts or by a different crane on the exterior of the building.
Methods
To start the solution process it would be a wise decision to discuss the architect’s main purpose for selecting the current system. Using this information to then cross reference this with the Owner’s desires for the project and initiatives for the futures will be important in determining what may or may not change based on the Clinic’s desires.
Next it would be important to determine if there is a way to modify the current system’s placement plan. There could potentially be a reason the construction team chose the current placement method but there may have been another method that would have worked better.
After looking at the placement process it would be wise to research similar systems that do not have as complex connection issues. A schedule and analysis of schedule impacts, other trade impacts, and cost impacts would need to be conducted to determine if this is a better alternative or if the impacts are not significant enough to make changes.
Expected outcome
It is expected that the solution will improve the constructability and quality control process of the curtainwall system. With a simplified process and easier implementation the schedule should be reduced for the placement of the curtainwall system and should ultimately shorten the project overall duration because trades would be able to have access to the floors sooner to continue work.
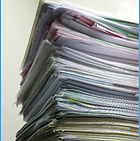
Analysis 2: Submittal Process
Background research
The submittal process on any job is a very important aspect of the building that needs to be completed and approved before any work could be started and any products may be use within the building. Not only is this process important to know what products will go into the building but it is also important to check if the product meets the owner's desires, designer's requirements, and code standards. The current submittal process contains steps that could be amended and altered to ultimately become more efficient.
The submittal process has come a long way from paper to electronic handoffs which has dramatically decreased paper waste, cut down on approval time, and created a better source for storing the project information throughout the construction process. Now it is time to revisit the process because it is effecting the project schedule and consuming much of the different project party’s time.
Another issue that has been emphasised was the length of certain submittal items and how downloading time and space on individual’s computers was not a favorable trait of the current process.
Potential solution(s)
This seemed to be a window of opportunity for the LEAN team on the Cleveland Clinic job site that could potentially eliminate unwanted waste on project schedule and employee man hours. It will be important to determine the key schedule impacts of the submittal process. Some potential solutions for this would be a solution that addresses the lag time between submittal handoffs. Having a submittal “chatroom” of some sort that would allow multiple parties to comment and input changes or approval at the same time to eliminate the saving and downloading process. This was a process that was introduced on the jobsite through Bluebeam studio and seemed to have some benefits but did not fully address all of the issues.
Another solution would be a system that kept priority submittals at the forefront of the submittal list to be addressed so that the submittals which are more urgent would be addressed first. This would eliminate “lost” or “forgotten” submittals and also help busy designers, contractors, and architects keep order of the project needs and priorities.
Another potential solution would be the idea of gathering a list of submittals and having weekly meetings to get submittals approved and pushed through to the rest of the project team. This would require a person to determine the necessary parties to be present during submittal reviews and also a relative quantity of submittals that are reasonable enough to review.
Methods
The first step in this process would be to gather information on the current submittal process and what seems to be the largest schedule impact. This could be done by looking at submittal release dates, durations between different party approvals, number of submittals that are approved the first time, number of submittals that get sent back for corrections and other information that is already tracked by the current submittal system.
After gathering the current submittal process durations, a decision on two to three of the most pertinent and time consuming tasks will be chosen for improvement. The solutions mentioned in the previous section will be addressed to see if they could potentially solve the issues. Also, other methods from projects that had a relatively successful submittal process will be researched and observed for the differences and how they were so successful in this process.
Expected outcome
The expected outcome of this analysis is to minimize project schedule impacts from slow approval of submittals. If the critical path of the project is not reliant on the submittal process, another desired and expected outcome would be to minimize the individual submittals approval time so that it is not lingering over the project team.
The priority submittals being approved first are also another expected outcome. An ideal submittal process would include the priority submittals approval even if other submittals were sent through to the project team first.
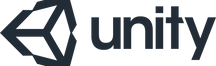
Research: BIM Beyond Construction
Industry Issue and Initiaves
As part of a large initiative at the Cleveland Clinic Cancer Center project ,LEAN design and construction has been the primary focus of the Owner as well as project team. Initiatives such as implementing the Last Planner System and bringing in LEAN specialists to observe and identify processes where waste can be minimized are a few ways the Cleveland Clinic Cancer Center project team are becoming more efficient.
As quoted from the LEAN Construction Institute webpage mission statement, "Lean theory, principles and techniques, taken together, provide the foundation for a different, more collaborative, and more effective form of project management". This statement is one reason which lead me to conducting research in facilities management. Taking the overall concept of LEAN I began to think of other matters in which waste could be eliminated. This lead to BIM and how it has brought huge savings to the construction industry as new and more advanced technology such as CAD, Revit, and other modeling tools have become more mainstream. The use of these technological tools has become a standard requirement for large projects in coordinating construction but has not been leveraged for post construction maintenance such as facilities management teams.
In conducting this researech I would need to reach out to the Clinic to investigate the current process of facilities management. After discovering this information I would need to focus on the information produced during construction and how that applies to facilities management. Looking into technological tools that could be leveraged in the transfering of this information will be done through Unity.
Cleveland Clinic Initiatives
Part of conducting this research will be to observe what the Cleveland Clinic's initiatives and vision are for the most optimal outcome of facilities management staff. Understanding the size, scale, and past project information provided will identify the next steps in adapting the future process and possibilities of facilities management.
Potential Solutions
Unity is a gaming software that has been adopted and designed for game creation. This software has the potential to be designed for process analysis and potentially construction industry management. Identifying the combatibilities of Unity, there may be some potential to leverage this gaming program for potential industry use.
By identifying the ideal desires of the clinic and Unity's capibilities, there is potential to discover combatible crossover. This would also be the utilization of the BIM technologies that are highly developed and adapted throughout construction for facilities management.
Expected outcome
In conducting this research it is expected that the Cleveland Clinic's initiatives will be identified. Creating a valid process map that clearly identifies the challanges and opportunities of Unity will be essential in leveraging the Unity protyping process.
Unity will be investigated and a prototype will be developed. With this prototype, a process map will be created to show the ideal functionality of the Unity prototype.
Breadth Technical Studies
Breadth 1: Structural
In addressing the first analysis of this proposal, there will need to be some structural research done to determine if a different support of excavation system could double as the proposed foundation system of this project. The current point loads on the steel structure would need to be obtained and then a proper method would need to be researched in order to properly implement this. As mentioned in analysis 1, the current support of excavation system serves no purpose after construction so if there was a way to tie in this system with a structural foundation system, the two separate costs of the two systems could be combined into one, multipurpose system that hopefully comes at a lower cost to the project. Because I will be looking at an alternative for the support of excavation system, I would like to look into the structural design of the alternative system and the strength the new system would need to obtain. One alternative system considered is a diaphragm wall. In order for this to work this would include research into a structural design of concrete and a rebar cage in order to fulfill proper strength. I would also look into the engineering already completed for the structure of the building and make sure the new system would fulfill these requirements.
Breadth 2: Acoustical
With the implementation of the third analysis in the curtainwall system the rooms that have the dividing wall would contain the connections that are intricate and may provide a sound leak. Because these rooms are infusion rooms, STC rating of the wall construction is very important. Other rooms that are affected by this are offices on the 5th and 6th floors of the building. These dividing wall assemblies could be constructed and an acoustical study could be done before and after the new proposed system is implemented in order to determine if changing this system would be better or worse for sound transmittance.